The construction of a wing panel with a symmetrical or semi-symmetrical airfoil presents a challenge: keeping the ribs in their proper position and keeping the wing straight. One cannot pin or attach wing ribs to a flat building board like you can with flat bottom wings. There are several methods to accurately build a wing with a curved bottom contour. Over a period of time I will describe several types of wing building and holding fixtures. The twin rod system is featured this month.
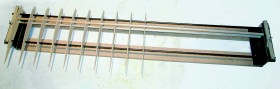
The twin rod system was first popularized by the Adjusto-Jig system introduced in the 1970’s. It was highly engineered with molded plastic parts. Even the wing dihedral could be set up with the wing accurately built in one piece. I have used several variations of this system with numerous model projects. The largest aircraft I have built using this kind of jig system were three 100-inch AL-1 all-aluminum aircraft I built about five years ago. I used 3/8- inch aluminum tubing for the two wing rods. I am currently designing an 83-inch Zlin 526AFS to be powered with a DA50. I am planning to use the Great Planes wing jig to build the stabilizer/ elevator and the fin/rudder assemblies for that plane.
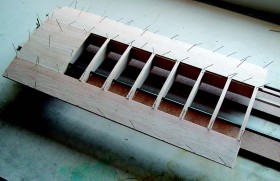
GREAT PLANES PRECISION WING BUILDING JIG
Lets take a look at the Great Planes Precision Wing Building Jig (Part No. LXK258, $17.99). The principle of the twin rod system is to place the wing ribs on two rods that are supported at each end. The two support brackets keep the rods in line with each other and also spaced equally apart.
Two alignment holes are carefully placed in the ribs. A simple drill jig or alignment fixture should be used to ensure that the rod alignment holes are correctly positioned when you drill the ribs. The 1/4-inch diameter alignment rod holes are generally located on the centerline of the airfoil. This location also makes it simpler to properly establish the correct incidence angle for the wing. The location of the two holes is critical in that they must be an equal distance apart and in a fixed horizontal and vertical location.
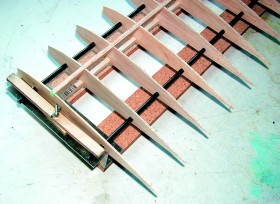
There is a minor amount of assembly required for the Great Planes jig. One has to screw the two formed aluminum end plates to the supplied particleboard bases. Two 6-32 clearance holes have to be drilled in the plywood rod hold-down plates. Maybe it takes 10 minutes maximum to get the jig ready. Assembly is simple.
Several Great Planes airplane kits have the wing ribs with wing rod holes already provided. If you’re curious, you can contact Great Planes to determine which of their kits offer this.
First, slide the wing ribs (with the wing rod holes) onto the two 1/4-inch diameter steel rods. Move the ribs to the approximate spacing required. At this point the rib locations are not critical. Next the wing rods are clamped to the aluminum end plates. The wing rod position should be parallel to the wooded base pieces. 6-32 screw and wing nuts firmly clamp the assembly in position.
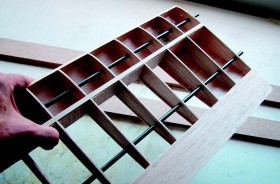
The wing spars will be used to place the ribs in the correct locations. Mark the locations of the ribs on the top spar(s). Hold the top spar in position and slide the ribs into position. Place the top spar(s) onto the ribs and make any final rib location adjustment as required. Place the bottom spar(s) in position. Check the alignment of the ribs to make certain they are vertical. Now glue the spars in to the ribs.
After the ribs are in position, with straight pins, glue the bottom part of the trailing edge sheeting in place, or if there is a rear aileron spar, glue it to the ribs. With a small square or drafting triangle, make certain that the ribs are perpendicular to the spars. Then glue the leading edge stock into position. I prefer to use Elmers white glue during the process as it gives you some time to realign the position of the ribs. CA glue can be used for most of the additional glue joints. If there are shear webs (vertical grain wood pieces that attach to the top and bottom wing spars) used in the design, then they should be installed at this time. This will eliminate any bending of the spar while it is in the jig.
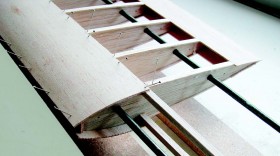
If shear webs are not used, then it would be a good idea to provide a support under the main spar to keep it from sagging or bending when the leading edge sheeting is applied. Glue the upper trailing edge and leading edge sheets in place. If cap strips (strips that run along the outside edges of the ribs, from the leading to trailing edge) are used, glue them in as well.
When the glue has dried, unclamp the wing rods from the aluminum plates. Lift the wing from the jig. Turn the wing panel upside down and reinstall it onto the wing jig and clamp it back in place. Now the bottom sheeting can be attached in a similar manner.
As one can see from the photos, building a wing panel on this type of jig is not difficult. Almost any type of wing panel can be built with this system. The jig design can itself be easily enlarged to the size necessary.
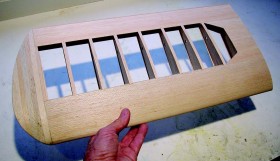
If the wing panel requires washout (wing tip rib trailing edge is raised slightly), then it is a simple matter to raise the tip wing rod slightly to provide the amount of washout needed. If the design of a tapered wing is such that you cannot place the alignment holes equidistant so the wing rods are parallel to each other, then one can have one (or both) of the wing rods at an angle. It is more difficult to locate the wing rod holes when this is done. I suggest that instead of a drilled hole for both of the rods you create a slot in the ribs for one of the rods. The other wing rod hole will be spaced at some fixed distance from a spar. This slot will allow for the angled wing rod to find its own location and your rib will still be properly aligned.
With a little bit or ingenuity, the tworod jig system can be used for fuselages as well. With two of the jigs joined together (including the dihedral) at the center of the wing, one could build both wing panels as a one-piece structure. However it is a lot easier to simply make two wing panels and then join them together. See you next month!
Links
Great Planes Model Manufacturing, distributed exclusively by Great Planes Model Distributors
www.greatplanes.com, , (800) 682-8948